7 min read
Redefining Modern Pipe Design With Finite Element Analysis
Paulin Research Group
Aug 28, 2024 10:13:24 AM
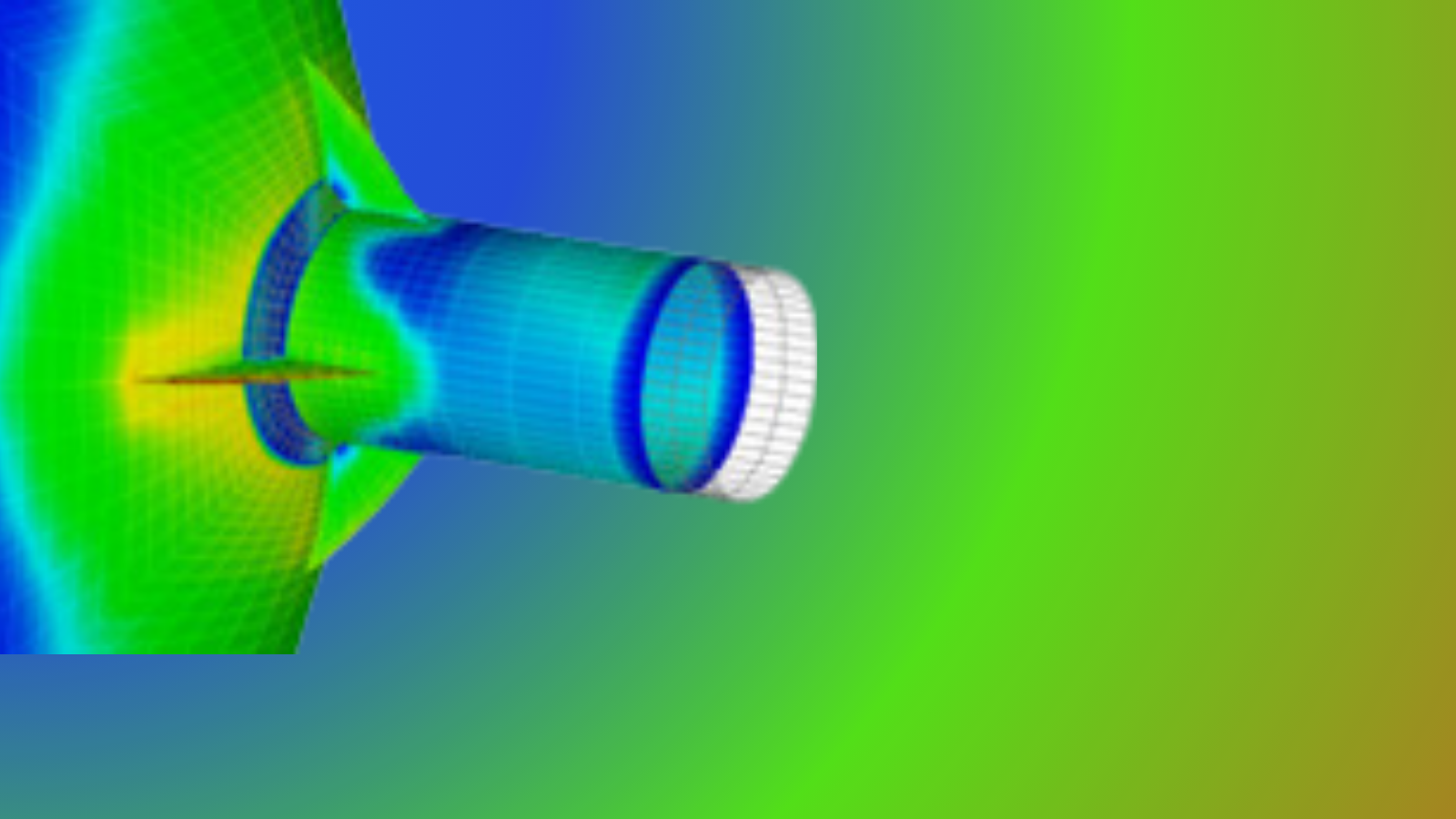
As piping systems advance, engineering methods must adapt to meet the changing demands. This was the key realization for Robert Weyer, Lead Piping Engineer at Amesk, who has spent years modernizing piping design and analysis approaches through the use of innovative Finite Element Analysis (FEA) software.
Piping design and construction is a complex field, and maneuvering through the intricacies of modern engineering often means grappling with codes that offer only minimal guidance. Robert has dedicated his career to bridging this gap by implementing advanced methods to solve today’s most pressing piping challenges. His work highlights the need to move beyond outdated techniques by leveraging modern software that not only expedites design processes but goes beyond vague guidance for B31.3 requirements outside of “shall be taken into account.”
Throughout his involvement in major LNG projects in Australia, Robert identified significant shortcomings in traditional design methods that fail to fully utilize the technological advancements available to engineers today.
Recognizing the importance of modern solutions, Robert has co-authored numerous papers, including one on improving risk management in pneumatic testing. His research highlights the critical need for updated practices, as industry codes may not always offer detailed guidance on every potential hazard. This has led Robert to advocate for the use of advanced software, such as Paulin Research Group's FEPipe and NozzlePRO, which offer more accurate modeling and analysis, ensuring safer and more reliable piping systems.
The Problem: Outdated Methods in a Modern World
The northern coast of Western Australia is home to abundant natural gas reserves, but the challenge lies in transporting this gas to distant markets, such as South Korea and Japan. To overcome this, Chevron has constructed two significant Liquified Natural Gas (LNG) plants: Gorgon on Barrow Island and Wheatstone near Onslow.
These plants convert natural gas into a liquid form for easier transport. The facilities include various complex systems, such as inlet facilities, LNG plants, condensate handling utilities, and storage and export units. Additionally, both Wheatstone and Gorgon provide natural gas to the domestic market, tying into the Dampier to Bunbury Natural Gas Pipeline (DBNGP) via a 44-mile sub-sea pipeline from Barrow Island.
However, the design and construction of piping systems in these LNG plants pose unique challenges that differ significantly from those in traditional petroleum refineries, which the B31.3 piping code was originally based on. Refinery piping typically deals with low-pressure, high-temperature liquid flows in carbon steel pipes. In contrast, LNG plant piping must handle high design pressures, cryogenic temperatures, and gas flows, often requiring the use of austenitic stainless steel. The large diameter pipes used in LNG plants, often exceeding DN1800, and with D/t ratios over 100, present additional challenges. These pipes operate under conditions that push the limits of conventional Stress Intensification Factors (SIFs) provided by the code [2].
Moreover, the use of stainless steel, necessary for its ductility at low temperatures, comes with higher costs. As a result, large pipes are often ordered to specific thicknesses rather than nominal ones, reducing the margin of safety that typically exists in carbon steel piping. High-pressure gas and high flow rates in LNG plants can also lead to significant vibration issues, a concern that the B31.3 code vaguely addresses, only stating that such factors "shall be taken into account."
Additionally, the two-phase nature of the flows can generate substantial fluid momentum loads, for which the code again offers limited guidance.
During his work on various LNG projects in Australia, Robert recognized that the traditional piping design methods, heavily influenced by refinery practices, were inadequate for the unique demands of LNG plant piping. These outdated methods fail to leverage the advanced capabilities of modern engineering software. Tools like those offered by Paulin Research Group, which utilizes finite element analysis (FEA), are better equipped to address these challenges. For existing plants, fitness-for-service (FFS) assessments provide a crucial means of ensuring continued safe operation, helping to avoid unnecessary and costly shutdowns.
ASME Research on Beam Vs Shell Modeling
Over the years, Robert has consistently contributed to the piping industry by publishing a series of conference papers that address emerging challenges in piping design and analysis. His work emphasizes improving design methods and ensuring the mechanical integrity and safe operation of piping systems through real-world examples and innovative approaches.
2018 Research: In his 2018 paper, Robert focused on the risks associated with pneumatic testing, particularly the dangers posed by fragment throw, which had been historically overlooked by industry codes. He highlighted a significant incident in 2009 at the Deep-Water Port construction site in Shanghai, where a pneumatic test explosion caused fatalities and injuries, underscoring the inadequacy of existing exclusion zone guidelines. Robert's research revealed that stored energy alone is an unreliable risk indicator, and he advocated for a deeper understanding of the scientific principles behind code requirements to enhance safety during pneumatic testing [1].
2020 Research: In his 2020 paper, Robert explored the unique challenges of LNG plant piping, which differs significantly from traditional refinery piping. He discussed how the B31.3 code, originally designed for low-pressure, high-temperature refinery systems, falls short in addressing the high-pressure, cryogenic conditions of LNG plants. Robert emphasized the need for engineers to account for additional loads and the reduced margin for error due to the use of stainless steel piping ordered to exact thicknesses [2].
2021 and 2022 Research: In his 2021 and 2022 papers, Robert delved into the advantages of using shell modeling over traditional beam element analysis for piping systems. His research demonstrated that shell models, coupled with modern finite element analysis (FEA) software like FEPipe, provide a more accurate representation of piping systems, especially when dealing with complex loads such as high fluid momentum. He also introduced improved methods for assessing slug loads and discussed the benefits of non-linear analysis in understanding the behavior of piping materials under extreme stress conditions.
These published findings reinforce Robert’s commitment to advancing piping design practices by leveraging modern engineering tools and addressing gaps in existing codes and standards [3], [4].
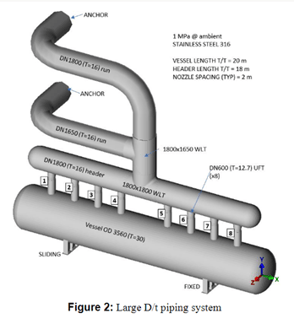
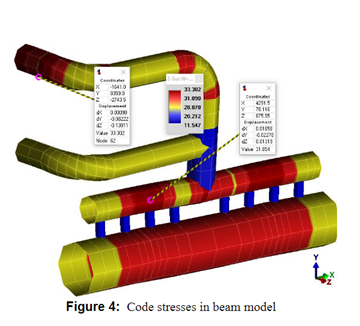
The Reality of Modern Piping and ASME B31.3
Robert’s extensive research and publications have highlighted a critical reality in the field of piping design: no single code, including ASME B31.3, can account for every potential load case a piping system might encounter. In instances where the code is silent, engineers often need to seek guidance from other codes or rely on a deep understanding of the principles underlying the design codes. This insight helps identify which failure modes the code aims to prevent, allowing for more informed decision-making.
In his more recent papers, Robert discusses the complexities engineers face in determining allowable limits, particularly when balancing competing requirements. For example, ensuring adequate flexibility in piping systems to accommodate thermal expansion and contraction has traditionally been a priority. However, recent failures due to excessive vibration have shown that too much flexibility can be just as detrimental. Similarly, piping systems must balance the need for sufficient flexibility with the ability to withstand high fluid momentum loads, which might only occur once. This scenario often requires non-linear analysis using shell elements to account for permanent deformation.
Beam Modeling Limitations: During his 2022 PVP Conference presentation, Robert explored the limitations of beam modeling in piping analysis. While beam modeling is a convenient and widely used method, it relies on Stress Intensification Factors (SIFs) that can be inaccurate, especially for complex geometries like pipe intersections. These SIFs, some of which date back to the 1940s and 1950s, have prompted the development of more accurate alternatives, such as ASME B31J, which has replaced the outdated Appendix D in the 2020 edition of B31.3.
Robert also noted that modern software tools, such as FEPipe and PCLGold, offer advanced capabilities that go beyond traditional beam modeling. For instance, the use of 18-degree-of-freedom beam elements allows for the evaluation of ovalization in piping, leading to more accurate stiffness calculations and better overall modeling accuracy. These tools enable engineers to address local bending stresses and other critical factors that beam models might overlook.
Shell Modeling Advantages: Shell modeling offers a more detailed approach by representing the actual pipe geometry and accounting for both membrane and bending actions. This method is particularly useful when dealing with large diameter-to-thickness (D/t) ratios, non-linear material behavior, or scenarios where rigid intersection assumptions are unrealistic. Shell models can identify highly stressed regions within the piping system, providing engineers with a clearer understanding of its behavior under various loads.
Beam Modeling |
Shell Modeling |
Traditional method | Advanced analysis capability |
Simplifies the pipe into a series of straight elements |
Accounts for the actual geometry of the pipe, including bends and fittings |
Quicker, less detailed analysis | Very detailed analysis |
Useful for straightforward piping systems not necessitating exact precision / not ideal for complex systems or non-linear materials | Useful for complex systems or extreme conditions |
Robert's 2022 paper concludes that while beam modeling is generally sufficient for most piping systems, there are situations where shell modeling is necessary to ensure the system can withstand anticipated loadings. Advances in software and hardware have made this kind of modeling more accessible, allowing engineers to achieve safe, code-compliant designs even for the most complex piping systems.
The Solution: Leveraging Advanced Software Tools
To solve these modern challenges, Robert turned to advanced engineering software, specifically the FEPipe and NozzlePRO solutions. These tools enable engineers to move beyond traditional beam-type analyses, which often fall short when dealing with complex geometries and dynamic loads, to more sophisticated shell-type modeling.
Shell modeling, in particular, allows for a more accurate representation of the piping systems, capturing local stresses and deformations that beam models might overlook. This is crucial when dealing with large-diameter piping or when the assumption of linear elastic behavior is insufficient, such as in cases involving high momentum slug loads or when non-linear material behavior needs to be considered.
By utilizing FEA through PRG's software, Robert and his team could address issues that the B31.3 code does not fully cover. For example, they could accurately assess the impact of high fluid momentum loads on piping systems, ensuring that the designs could withstand these loads without catastrophic failure.
Real-World Application: Enhancing LNG Plant Safety
Robert's work didn't just stay theoretical; it had real-world applications that significantly improved the safety and reliability of LNG plants in Australia. His research, presented at various ASME Pressure Vessel and Piping (PVP) Conferences, provided detailed examples of how modern FEA tools could be used to better manage the risks associated with pneumatic testing, high-pressure piping, and other critical aspects of LNG plant operation.
For instance, his 2018 paper highlighted the dangers of fragment throw during pneumatic testing, a risk that industry codes had historically overlooked. By applying FEA and shell modeling, he demonstrated how engineers could better predict and mitigate these risks, potentially saving lives and preventing costly accidents.
Modern Problems Require Modern Solutions
Robert's work emphasizes an important lesson for the engineering community: as the challenges faced by modern industries evolve, so too must the methods and tools used to address them. Traditional methods, while still valuable, need to be complemented with advanced technologies like FEA to ensure that piping systems are safe, reliable, and compliant with modern standards.
By adopting these modern solutions, engineers can not only solve today's most pressing problems but also anticipate and mitigate the challenges of tomorrow.
References
[1] Weyer, R., Arti, B., Dang, T., & Taagepera, J. (2018). PNEUMATIC TESTING OF PIPING MANAGING THE HAZARDS FOR HIGH ENERGY TESTS. PVP Conference, 15 July 2018, Prague, Czech Republic.
[2] Weyer, R. (2020). IMPROVING LNG PLANT PIPING (OR HOW LNG PLANTS ARE IMPROVING PIPING). PVP Conference, 20 July 2020, Virtual, Online.
[3] Weyer, R. (2021). ASSESSMENT OF DYNAMIC HIGH MOMENTUM SLUG LOADS ON PIPING FOLLOWING THE TUBE RUPTURE. PVP Conference, 12 July 2021, Virtual, Online.
[4] Weyer, R. (2022). OVERVIEW OF PIPING STRESS ANALYSIS USING SHELL ELEMENTS. PVP Conference. 17 July 2022, Las Vegas, Nevada.
[5] Chevron Policy, G. and P. A. Gorgon Project. https://australia.chevron.com/our-businesses/gorgon-project. 2022, February 22.