5 min read
Finite Element Analysis in PVP Design: What You Should Know
Paulin Research Group
Nov 21, 2024 1:46:34 PM
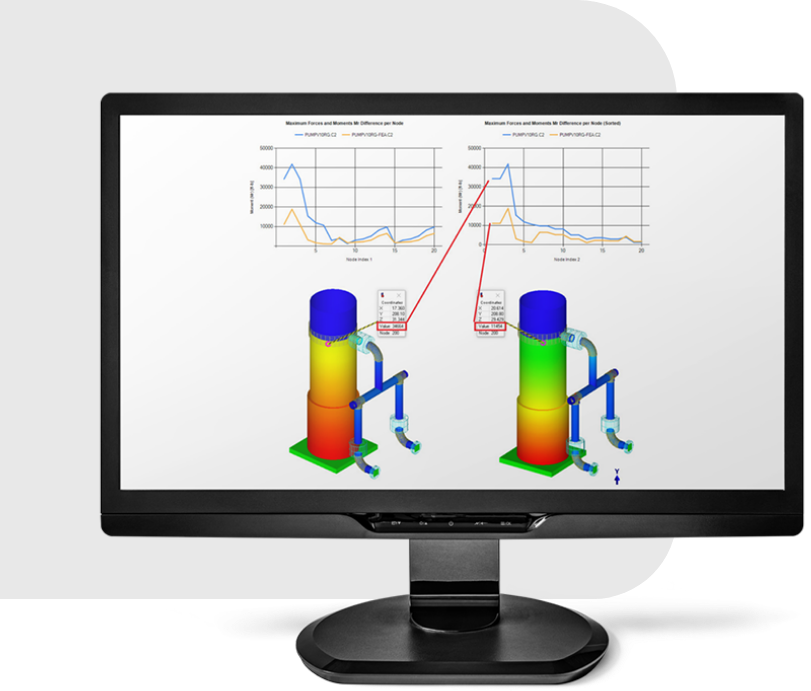
In pressure vessel and piping (PVP) design, various analysis methods are used to assess the safety and performance of systems. While hand calculations and simplified Design by Rule (DBR) methods are effective for straightforward designs with basic geometries and uniform loading, they can become limiting when applied to more complex systems involving non-standard geometries, transient material properties, and dynamic conditions.
In such cases, Finite Element Analysis (FEA) offers a more powerful and flexible approach. FEA allows engineers and designers to more accurately model and assess the performance of pressure vessels and piping systems under real-world operating conditions, making it an essential tool for more demanding design challenges. Paulin Research Group offers specialized FEA solutions, including NozzlePRO, FEPipe, and PVPTPro, each tailored to address specific complexities in PVP design.
The Role of Finite Element Analysis in PVP Design
By discretizing a complex structure into a mesh consisting of smaller and simpler parts called finite elements, FEA enables engineers and designers to closely predict stress, strain, and failure points—critical for ensuring the safety and performance of these systems.
Key Benefits of FEA in PVP Systems
- Complex Geometries: FEA can model intricate features relating to nozzles, welds, and supports that are difficult to handle with simpler analysis tools. Tools like NozzlePRO offer specialized FEA for nozzle and attachment load analysis and more accurately common and necessary pressure vessel design problems, which traditional methods may not fully capture.
- Accurate Stress Results in Critical Areas: FEA provides users with precise stress, strain, and deformation predictions. Software like FEPipe applies FEA to larger vessel models and piping systems, allowing engineers and designers to assess stress results across larger systems, accounting for factors like wind and seismic loads, thermal expansion, and external forces.
- Nonlinear Material Behavior: Nonlinear FEA captures the responses of a complex structure due to material nonlinearity, geometric nonlinearity (or the combination of both), and is crucial for analyzing fatigue, yielding, and thermal effects in pressure vessels and piping. FEPipe supports nonlinear analysis of a structure subject to both elastic-plastic and large displacement/rotation deformation so that users can see the predicted flaws and cracks through Level 2 and 3 fitness-for-service analysis. It also performs automated nonlinear Sustained Stress Indices (SSIs) and collapse calculations for shell geometries, ensuring an accurate assessment of material behavior under complex loading conditions.
- Thermal and Pressure Effects: FEA simulates the impact of thermal gradients and internal pressures or vacuum, helping predict expansion, deformation, and failure risks. NozzlePRO accurately models the combined effects of thermal, pressure, and external loads on nozzles, properly considering loading cycles, fillet weld design, and transient effects to ensure precise stress analysis and compliance with industry codes.
- Fatigue Analysis: FEA identifies fatigue-prone areas and predicts the lifespan of components under cyclic loading. FEPipe supports this with both linear and nonlinear fatigue assessments on nozzles and attachments, helping users address common design issues in piping and pressure vessel systems.
Model in FEPipe
When to Use Traditional Methods
Traditional methods, such as hand calculations, simplified Design by Rule methods, and basic software tools, have long been used in the design and analysis of pressure vessels and piping systems. These approaches work well for straightforward cases with standard geometries and loading conditions. However, as PVP designs become more intricate—due to factors like complex geometries, non-linear material behaviors, or dynamic loading conditions—traditional methods may be less effective.
Consider, for example, a pressure vessel with nozzle clusters with external loads, complex internal structures, and dissimilar material properties. While hand calculations and rule-based methods can provide rough estimates, they often rely on simplifying assumptions. These might include uniform material properties, idealized stress distributions, and basic geometry, all of which can overlook critical aspects of the design.
For instance, stress concentrations at nozzle connections or the impact of welding process can lead to inaccurate predictions of component performance and failure risks. Thus, these methods may lack the precision needed for safe and reliable design in more complex PVP systems.
When FEA Goes Beyond Traditional Approaches
FEA offers more tools for analyzing complex pressure vessels and piping systems. By discretizing the structure into small elements, FEA allows engineers and designers to better simulate how the entire system behaves under real-world loading conditions. FEA helps users achieve a more realistic and comprehensive understanding of structural performance.
When designing pressure vessel and piping systems, it’s useful to compare different common methods to understand their unique applications. The table below displays the key differences at a glance.
Type |
FEA |
Hand Calculations |
Simplified Rule-Based Methods |
WRC 537/107 |
WRC 297 |
Complex Geometry |
Accurate modeling of complex geometries with flexibility and detail. |
Limited to simple standard geometries; often relies on idealized assumptions (e.g. simple shapes such as cylinders, flat plates). |
Some can handle complex shapes, but intricate features are simplified or approximated. |
Focuses on nozzle and attachment analysis in thin-walled cylinders, spheres or ellipses. |
Limited to cylinder-to-cylinder geometries. |
Material Behavior |
Can model both linear and nonlinear behavior, including plasticity, fatigue, and other material nonlinearities. |
Typically assumes linear elasticity, no accommodation for plasticity or fatigue (idealized material behavior). |
Linear elasticity is typically assumed; some codes may incorporate nonlinear material models in specific cases. |
Linear elasticity assumed; works for typical materials used in thin-walled pressure vessels or piping. |
Linear elasticity assumed; suited for typical materials in thin-walled pressure vessels or piping. |
Loading Conditions |
Handles static, dynamic, thermal, and time-dependent loads with high fidelity. |
Assumes static loading with uniform pressure, forces, and idealized boundary conditions. |
Primarily static loading; some codes can handle simplified dynamic conditions. |
Static external loading only, no pressure or more complicated loading. |
Static external loads and internal pressure only. |
Stress Concentrations |
Accurately captures stress concentrations at critical locations. |
Uses approximate solutions based on simplified formulas (e.g., stress concentration charts. |
Uses stress concentration factors, which may be conservative or imprecise for complex geometries. |
Simplified approximation--but reasonable for the supported geometry. |
Simplified approximation--but reasonable for the supported geometry. |
Dynamic |
Capable of simulating dynamic, transient loads, vibrations, thermal cycling, etc. |
Not suitable for dynamic or transient analyses due to simplifying assumptions. |
Limited dynamic analysis capabilities; typically for simplified dynamic conditions like resonance or simple vibrations. |
Not suited for dynamic loading or transient conditions; static-only analysis. |
Not designed for dynamic or transient conditions; static analysis only. |
Anticipating Changes & Advancing FEA in PVP Design
As pressure vessel and piping designs continue to advance in complexity, finite element analysis (FEA) is becoming an increasingly essential and powerful tool in their design and evaluation. Often, FEA results require review and approval by a certified Professional Engineer (PE) to ensure compliance with safety and regulatory standards. While PE oversight remains critical for high-risk designs, advancements in FEA tools are streamlining workflows for less critical scenarios. These improvements, along with growing confidence in validated models, are driving changes in regulatory frameworks, reducing PE involvement in standardized or lower-risk applications.
Modern FEA tools like NozzlePRO, FEPipe, and PVPTPro are at the forefront of this technological innovation. They provide engineers and designers with advanced insights to tackle intricate geometries, complex load conditions, and nonlinear material behaviors with precision and reliability. To recap:
- NozzlePRO simplifies nozzle connection analysis by automating ASME-compliant FEA and providing linear elastic and nonlinear solvers for accurate stress and collapse load predictions. With smart features like Vessel Link, analyzing design files from DesignCalcs, Finglow, Codeware Compress, and other software supports quick and easy FEA for almost any geometry.
- FEPipe offers a template-based approach tailored for rapid geometry construction and code-compliant results for pressure vessels and piping systems under complex loads, ensuring ASME BPV Section VIII Division 2 compliance.
- PVPTPro enables the simultaneous evaluation of multiple nozzles all under pressure and external loads, surpassing traditional methods like WRC 107, 297, and 537, and optimizing design performance with efficient FEA workflows.
By combining user-friendly interfaces with cutting-edge FEA capabilities, these tools help designers, engineers, and stress analysts address modern PVP challenges with confidence, reliability, and efficiency.
For more on anticipated code changes, visit our PVP Code Calendar or connect with our experts to explore how these tools can elevate your designs.