4 min read
Maximizing Equipment Life: The Crucial Role of Fitness-for-Service in PVP Engineering
PRG
Dec 1, 2023 12:28:15 PM
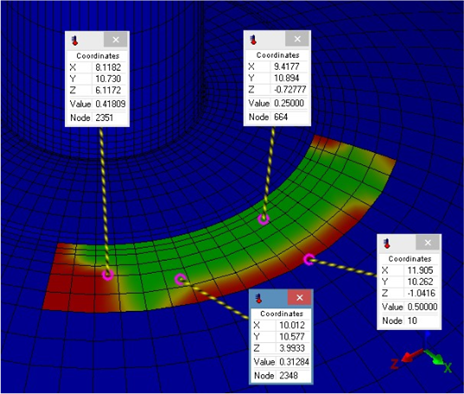
As reliability engineers, the design, analysis and maintenance of pressure vessels and piping systems is usually a part of the job description. Going a step further, ensuring the integrity and safety of these components is a complex task that can often demand advanced tools and methodologies. One such critical aspect is properly performing fitness-for-service (FFS) in pressure equipment, tanks and piping to determine how corrosion, thinning, cracks and other flaws affect the remaining life of the objects. Luckily, software exists today with embedded FFS analysis capabilities to make these determinations much simpler.
Without a doubt, this technology plays a pivotal role in maximizing operational efficiency, minimizing downtime and ultimately ensuring the safety of major assets and personnel. In the following blog, we’ll discuss the importance of FFS evaluations and provide some notes on how to produce the best, most accurate results.
Understanding Fitness-For-Service
Fitness-for-service is a comprehensive engineering evaluation methodology used to assess the integrity of in-service equipment. This includes pressure vessels, piping systems, tanks and other components subjected to various loading conditions, such as internal pressure, external pressure (vacuum), temperature gradients and external forces.
The main objective of a FFS analysis is to evaluate flaws in pressure vessels, piping and storage tanks to determine if they can remain in service. By its nature, the FFS procedure is intended to be conservative, although the conservatism can be reduced as the detail of the analysis is improved.
FFS evaluations can be performed on finite element analysis (FEA) models without cracks or local thin areas. Approximations can be made using the local nominal stress field to compute the stress in the crack or local thin area. FFS evaluations can also be performed on models that include simulation of the cracks or local thin areas and the stresses in the crack or thin area computed directly. This type of simulation requires greater knowledge of FEA.
The goal of FFS is to determine if existing flaws, damage or degradation in the equipment can be tolerated without compromising safety and functionality.
The Importance of Accurate Fitness-for-Service Evaluations
Without accurate FFS evaluations, industrial facilities are risking safety, operational costs and even the chance of being shut down unexpectedly for not following required code regulations.
Safety: Typically, an FFS evaluation is performed on a component that is either in service or has recently been in service when a crack or flaw has been detected. Usually, these flaws are already known, and the flawed component can remain in service providing the flaw has not increased in size since the system was last operated. For this reason, the percentage of the load reduction is often warranted when flaws are detected and before they are thoroughly evaluated. However, growing cracks can produce more significant problems because in a system that cycles regularly the flaw may increase in size so much so that the system will become unstable and ultimately fail. This is one of the reasons that growing cracks are particularly dangerous and difficult to evaluate effectively.
By identifying these potential failure points, operators can take proactive measures to prevent catastrophic incidents, ensuring the safety of the facility and its workers.
Optimized Maintenance Strategies: Traditional maintenance practices often involve unnecessary shutdowns and inspections, leading to increased downtime and associated costs. By accurately evaluating the condition of equipment, operators can prioritize and schedule maintenance activities based on actual needs, minimizing downtime, allocating resources where most needed and maximizing production output.
Compliance with Regulations: Adherence to industry codes and standards (such as API 579/ASME FFS-1) is a crucial requirement for any industrial facility. Fitness-for-service assessments help ensure compliance with regulatory requirements by providing a systematic and rigorous evaluation of equipment integrity.
This not only helps in meeting legal obligations but also contributes to building a culture of safety and reliability within the organization.
Some FFS Considerations from our experts
When the consequences of failure are high, multiple FFS calculations should be performed on the same flaw in hope that each method, conservative in its own way, can predict that a reasonable safety margin exists when the component is operating.
Engineers must recognize that some flaws are difficult to characterize while others are more typical. For example, the depth of microbial-induced cracking and some chemically-induced cracking can be difficult to characterize. The local properties of welds can be difficult to evaluate when pinhole leaks, contaminated weld pools or difficult welding positions can combine to produce locally weak areas in the weld where leaks are possible.
Additionally, here are some special considerations when performing FFS assessments:
- Local thin areas are usually easier to evaluate than crack-like flaws and are controlled by local failures or pressure boundary loss.
- When easy-to-size cracks in highly-ductile, commonly-used materials are in service over 150°F and are not subject to high rates of grain boundaries, they are usually controlled by local failures or pressure boundary loss, similar to local thin areas, making it easier to evaluate. Cracks and local thin areas whose longest length meridionally or circumferentially in a pressurized geometry is smaller than (RT)0.5 are considered easier to safely classify than cracks and local thin areas whose characteristic lengths are greater than (RT)0.5.
- Cracks and local thin areas whose depths are less than halfway through the wall are safer to classify than cracks and local thin areas more than halfway through the wall of the geometry.
- Cracks in geometries whose thicknesses are less than 1/4” to 3/8” are difficult to classify because the tolerance on most crack depth evaluations is a significant percentage of the plate thickness (in these cases a leak-before-break calculation should also be considered).
- Local thin areas are typically easier to conservatively classify if the thinnest local areas are larger than 0.25” in diameter. When very local thinned areas that are pit-type (less than 0.25” in diameter) are present in a locally thinned zone, API-579/ASME FFS-1 should be consulted. Pits are considered more critical when the pit ligament is less than 20% of the locally thinned wall. Pits usually occur in groups and in areas of associated local metal loss.
- Cracks in thick geometries have the lowest resistance to crack propagation and tend to be the most brittle.
- Detailed cracking in welds may involve the evaluation of numerous factors including voids, impartial penetration, residual stress states, the depth of the crack, the pre-cracking R ratio, overstrength and the number of passes. Additionally, the user is still responsible for determining critical J-factors for cracked geometries.
FFS Capabilities in PRG software
Among a variety of other capabilities, in FEPipe and NozzlePRO, PRG offers simplified Level 1/2 calculations that do not involve modeling of the flaw as well as less simplified Level 2/3 calculations that do involve modeling of the flaw to help users accurately determine the local thin areas and cracks in just a few clicks. The main focus of FFS evaluations in PRG software is to accurately and quickly assess:
- Individual components,
- Multiple components at once,
- Nozzle geometries and structural attachments on heads, cones and cylinders,
- Bend with supports (trunnions/stanchions and structural attachments) unreinforced, pad reinforced, contoured/welding tees and olet-type intersections and
- Other components and connections within the entire piping system.
With capabilities that go beyond traditional design and maintenance approaches, our goal is to offer engineers and designers a dynamic and risk-informed methodology for ensuring the integrity of in-service equipment.
By prioritizing safety, optimizing maintenance practices and minimizing costs, FFS capabilities contribute significantly to the overall efficiency and sustainability of industrial operations.
Request a consult today to see a live demo of our FFS analysis options.