3 min read
Understanding Cyclic Behavior and Ratcheting Analysis: Advancements
Paulin Research Group
Mar 5, 2025 11:20:55 AM
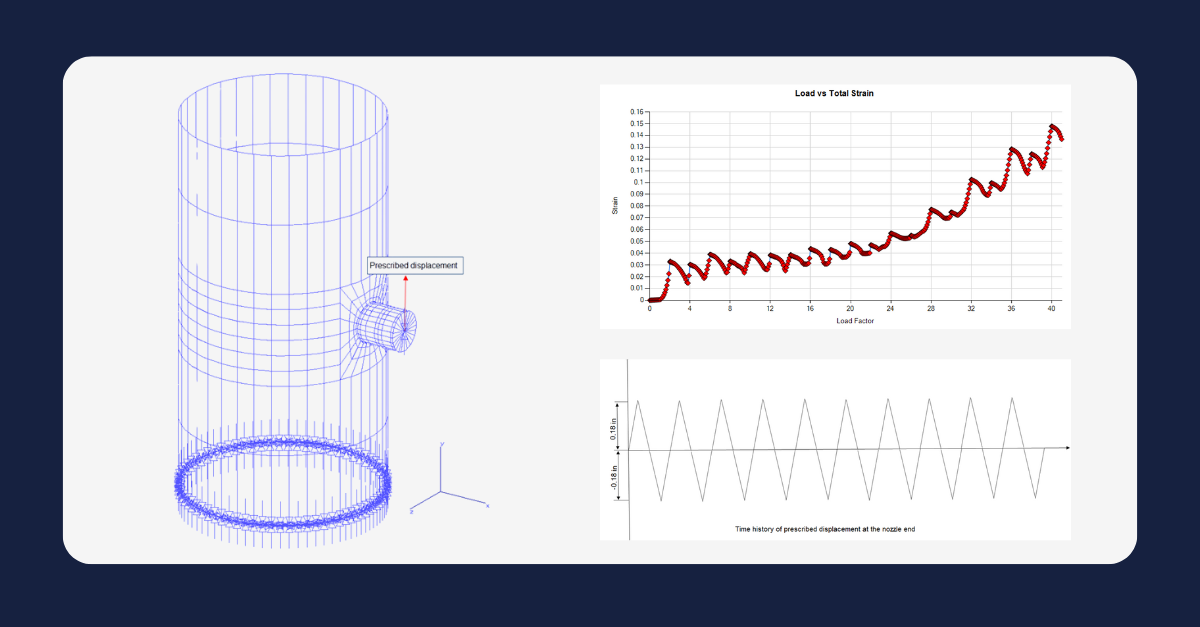
Ratcheting is a critical failure mode in pressure vessels and piping systems, occurring when progressive and incremental plastic strain accumulates under cyclic loading.
Simply put, when a structure undergoes repeated loading and unloading, it may gradually strain a little more with each cycle. For instance, as shown in the figures below, ratcheting occurs when a bar with bilinear kinematic hardening is subjected to a cyclic stress with a non-zero mean stress. Over time, this can lead to structural instability, accelerated fatigue, and even collapse.
Addressing this phenomenon is essential for ensuring the integrity and longevity of critical components.
Figure 1: Uniaxial Bar Subject to Cyclic Stress with Non-zero Mean Stress
Figure 2: Stress-strain Curve Response
ASME Approaches to Ratcheting Analysis
To mitigate risks associated with ratcheting, ASME specifies two general approaches for analysis:
1. Elastic Stress Analysis Approach
This approach is based on linear elastic stress analysis to check if the structure will shake down to purely elastic deformation after a few cycles. If the stress range remains within allowable limits, the structure is expected to resist progressive plastic strain and avoid ratcheting.
2. Elastic-Plastic Stress Analysis Approach
When elastic limits are exceeded, a nonlinear elastic-plastic cyclic analysis is necessary to directly simulate the structural response. The elastic-plastic analysis results can help determine whether the component will ratchet. The acceptance criteria defined in the code are as follows:
- No plastic action occurs.
- An elastic core exists within the primary-load-bearing boundary of the component.
- No permanent change in the overall dimensions of the component exists.
With PRG's upcoming release, estimated at the end of March 2025, these enhanced ratcheting and fatigue evaluation capabilities will provide engineers with a holistic approach to structural integrity assessment due to cyclic loadings. In our upcoming release, we provide engineers with an option to perform a ratcheting elastic-plastic analysis per ASME Section VIII, Div 2, Part 5. Our insights, along with the plotted geometry within our software, allow the engineer to make an informed decision on whether their component will pass per code.
This ensures compliance with the code while enhancing the safety and reliability of pressure vessels and piping systems.
Nonlinear Ratcheting Analysis: Advanced Engineering within PRG
Paulin Research Group has incorporated significant features in ratcheting analysis, leveraging the capabilities of FEPipe, NozzlePRO, and PVPTPro. These tools offer nonlinear analysis to evaluate cyclic loading effects and predict ratcheting behavior with greater accuracy.
Specifically, within PRG software, the analysis is provided to the engineer based on the elastic-plastic approach. The software provides four distinct ratcheting analysis cases as shown below, allowing engineers to simulate and evaluate different cyclic loading conditions effectively depending on the specific operating condition of the piping or vessel component.
Note: Prim denotes the primary static loading while Rng denotes the cyclic loading.
Figure 3: Ratcheting Analysis Options in Paulin Research Group Software
As mentioned above, users can select the ASME 5.5.7 Guidance for Ratcheting Cases option to run an elastic-plastic analysis per code in the next release. The software walks the user through this analysis and ensures that the output is extensive enough for the engineer to determine whether the component ratchets.
Figure 4: Ratcheting Cases Option in PRG Software
In one such analysis, the model featured below was subjected to internal pressure as the primary load, while a prescribed displacement was applied along the vertical direction at the free end of the nozzle, simulating the nozzle’s attached piping thermal expansion and contraction during an operating cycle.
This simulation included ten cycles of loading and reverse loading. As observed in the strain response plot, strain accumulation progressively increased with each cycle, demonstrating the ratcheting effect.
.png?width=1200&height=627&name=Ratcheting%20blog%20image%20(5).png)
Figures 5-7: Model in FEPipe with Load and Displacement Analysis
Comprehensive Fatigue and Structural Integrity Analysis for Pressure Vessels
PRG solutions provide engineers with a holistic approach to structural integrity assessment by combining ratcheting and fatigue evaluation. This ensures compliance with ASME codes while enhancing the safety and reliability of pressure vessels and piping systems, even under demanding cyclic loading conditions. To support these critical evaluations, PRG offers advanced fatigue analysis methods:
- Fatigue Assessment - Elastic Stress Analysis – Assesses fatigue life based on stress cycles, assuming purely elastic behavior.
- Fatigue Assessment - Elastic-Plastic Stress Analysis – Incorporates nonlinear material behavior for more accurate fatigue damage predictions.
PRG continues to provide more tools for ratcheting and fatigue analysis by incorporating advanced nonlinear simulation techniques. By utilizing FEPipe, NozzlePRO, and PVPTPro, engineers can model real-world loading conditions more accurately, mitigate risks, and enhance the safety of their designs.
For engineers facing challenges with cyclic loading like fatigue or ratcheting, PRG solutions offer the tools needed to navigate complex structural behaviors with confidence. Be among the first to experience these cutting-edge capabilities—schedule a discovery call today or request a personalized demo to see how PRG's next release can optimize your pressure vessel and piping designs.