4 min read
Faster FEA: Structured vs Unstructured Meshing
Dr. Delin Wang, Ph.D - Aerospace Engineering
Apr 17, 2023 2:52:20 PM
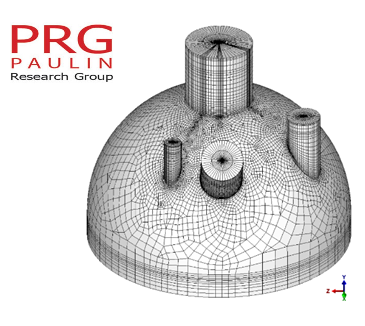
In finite element analysis, two types of meshes, structured and unstructured, are commonly used to represent a geometric domain by smaller discrete grid cells. The main difference between the two is the regularity and organization of the grid cells. As differences exist within each, so do their advantages. But mostly, the choice of either depends highly on the specific geometry and the time and resources available to analyze the model.
In the following blog, you'll read more about the benefits of using structured and unstructured mesh modelers to rapidly produce verification results for your pressure equipment.
Understanding Structured and Unstructured meshing
As mentioned before, when performing finite element analysis, both structured and unstructured meshes are commonly used to represent a geometric domain by smaller discrete grid cells.
Structured Mesh
A structured mesh consists of a regular and structured arrangement of cells, which are typically quadrilaterals or hexahedra in two and three dimensions, respectively. The sides of the cells are usually parallel, and the grid spacing is uniform. With this type of mesh, both advantages and disadvantages can occur.
Advantages
- Easier mesh generation
Structured meshes are easier to generate, as the grid cells have a regular and structured arrangement that can be generated automatically. - Faster numerical solutions
The regularity of the structured mesh can lead to faster numerical solutions, as the computation of the finite element solution can be simplified. - Better accuracy in simple geometries
Structured meshes can provide more accurate solutions in simple geometries, where the regularity of the mesh can help to reduce errors caused by distorted cells. - Lower computational cost
Due to the regularity of the mesh, the computational cost of solving the finite element equations is usually lower for structured meshes compared to unstructured meshes.
Disadvantages
- Limited flexibility
The regularity of the mesh can limit its flexibility in conforming to complex geometries or regions with curved boundaries.
- Increased computational cost in regions where the solution is smooth
The uniform spacing of nodes in structured meshes can lead to an excessive number of nodes in regions where the solution varies smoothly, which can increase computational costs.
- Less accurate with complex geometries
Structured meshes may not be able to provide accurate solutions in complex geometries or regions with curved boundaries, as the regularity of the mesh may not be able to conform to the shape of the domain.
Unstructured Mesh
Unstructured meshes, on the other hand, have an irregular arrangement of grid cells, which can be any shape and size. The cells can be quadrilaterals and triangles in two dimensions, hexahedra and tetrahedra in three dimensions, and the grid spacing is not uniform. Both advantages and disadvantages occur here as well.
Advantages
- Flexibility
Unstructured meshes are more flexible and can adapt to complex geometries and regions with curved boundaries, providing accurate solutions in these cases.
- Accuracy
Unstructured meshes can provide more accurate solutions in areas of the domain where the solution varies rapidly or where there are sharp gradients.
- Reduced computational cost
Unstructured meshes can reduce the total number of nodes required to represent the solution compared to structured meshes, which can lead to lower computational costs.
Disadvantages
- Difficulty in mesh generation
Unstructured meshes can be more difficult to generate and require more manual intervention, which can be time-consuming.
- Complexity
The irregularity of the mesh can make it more difficult to ensure accurate solutions, as errors can be introduced by distorted cells.
- Increased computational cost
Unstructured meshes can lead to increased computational costs due to the non-uniform spacing of nodes, which can lead to difficulties in numerical integration.
So What Do I use for my geometries?
Overall, the choice of whether to use a structured mesh or unstructured mesh depends on the specific geometry of the problem being analyzed, as well as the available computational resources and time constraints.
In general, unstructured meshes are more suitable for complex geometries with irregular boundaries, where they can provide accurate solutions while reducing computational costs.
so what Tools can Help with this while reducing my time and costs?
Paulin Research Group's latest release now includes a model-dependent unstructured mesher, which is accessible in PVPTPro, FEPipe and NozzlePRO.
In a nutshell, here's what it includes:
- An updated weld contour model to more accurately compute stresses in branch-to-run weld junctions.
- A localization mesher (developed by Dr. Delin Wang) to produce regular discontinuity grids around each nozzle or structural shape whose size is a function of (RT)0.5, local diameters and discontinuities.
So what can I accomplish with this?
PRG or Ansys
The updated weld contour model is used in the software automatically. Contoured shell elements from the penetration line to the toe of any connecting fillet are sized so that the rotational shell model inertias match those of the actual tapered volumetric geometry creating a more accurate local stiffness at any nozzle-shell intersection.
What's more is that these models can be exported to Ansys via the /PREP7 interface, thus preventing Ansys users from manually computing and reproducing these contours in Ansys shell models of branch connections.
Better Grid Localization with PVPTPro, FEPipe and NozzlePRO
The grid localization feature should be used for all PVPTPro models and for FEPipe and NozzlePRO models when the user requests unstructured meshing or when the unstructured mesh modeler is automatically selected by the software.
Localization incorporates a uniform regular mesh inside an unstructured mesh in most areas of the model with refinement only in particular cylindrical extents.
The Point: More Accurately Computed Stress and Verification Results
The structured regular mesher observes the (RT)0.5 sized interaction regions around nozzles in close proximity producing more uniform stress distributions regardless of the potential irregularity of surrounding models.
The user can still control mesh densities, and further, any irregular unstructured meshing in PVPTPro can usually be resolved by increasing the overall mesh density. Users should find, however, that solutions in the vicinity of nozzles and other discontinuities converge well before the surrounding mesh takes on a uniform appearance.
In this sense, PVPTPro can and should be thought of as a NozzlePRO for multiple nozzles. Large elements and zones are used in large areas of the model that are then removed from discontinuities and thus improves model efficiency.
Since NozzlePRO deals only with individual nozzles, structured meshes can typically be used to appropriately place elements around the penetration line and simulate weld leg contour thicknesses. And since PVPTPro deals with single or any number of nozzles, unstructured meshes can be used with the localization option to compute accurate stresses around all nozzles regardless of the unstructured mesh in areas far removed from the discontinuity.
With smart FEA software, there are benefits of using structured and unstructured mesh modelers to rapidly produce verification results for your pressure equipment.
Request a consult today to further see how this works in action.